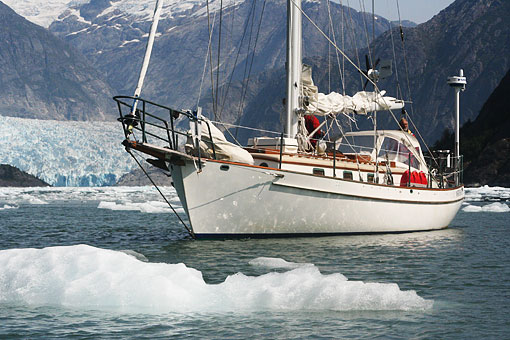
photo from the Cape George site
Cape George Marine Works continues to build blue water boats, even in a down economy. The following article was written by Diana Talley and published in the Port Townsend Marine Trades Association newsletter. You can download the entire newsletter here.
Todd and Tim Uecker of Cape George Marine Works have developed a business plan that really works. Their full service boatyard offers; boatbuilding in fiberglass and wood, fine cabinetry/joinery, design, fiberglass repairs, a boat yard and inside storage for do-it-yourselfers. Tim’s separate metal fabricating business – Meridian Stainless – makes you wonder why nepotism is a bad word.
Owning property just out of town, they keep their overhead costs down and never have to worry about landlords raising their rates. Their small crew has been working together for years with flexible work schedules, no turn-over, and an easygoing, professional work environment that clearly shows the benefits of teamwork in the quality they produce.
Larry Grobe specializes in laminating, Jason Gunby – fine woodworking, Bill Colson – all-around systems guy, and Ryan Chadwick (recent Boat School grad) is learning the business from all the angles. Geoff Custer is assisting with electrical design on their current project.
Cape George Cutters are known around the world for their sea-kindliness and
pedigree. The new big boat under construction is a 45 ‘pilothouse cutter loosely based on the Cape George 40. Designer Carl Chamberlin, reworked the design, adding 5 feet, adjusting the shear, and developing an interior to the specific needs of the customer, a fella from Oregon. What makes this boat so special is the owner’s inspired state of the art electrical system.
Basically it will be driven by an 18kw, 144 volt D.C electric motor connected to the
shaft and propeller with no transmission. A diesel gen set will charge the bank of batteries, as needed, but 3 – 4 hours of electric-only motoring is expected of this system. The 500 pounds of lithium iron phosphate batteries will produce as much electrical energy as 2000 pounds of traditional lead acid batteries. Prop assist generation under sail also will assist with battery recovery. Electric Marine Propulsion from Florida will be installing this system.
All of the boat’s appliances will be AC and use big inverters along with the Can bus
electrical distribution network supplied by BEP Marine of New Zealand. This cutting
edge automotive industry technology is making its way into the marine world. The
system features in line computer switching that allows control of all electrical needs at every appliance location. It reduces the burden of running heavy power lines to each location and then back again to a traditional fuse box, lessening the weight of wiring in this application by 500 pounds.
Todd estimates the project to be two years out as the owner is taking a slower, more sustainable approach to the costs of the building. So in their idle moments, the brotherhood is two weeks into their next boat building project: a 28’ Lyle Hess Bristol
Channel Cutter. This spec boat will be built as a finished hull only and wait until the right person buys it as is or has them complete it. What a great business plan!